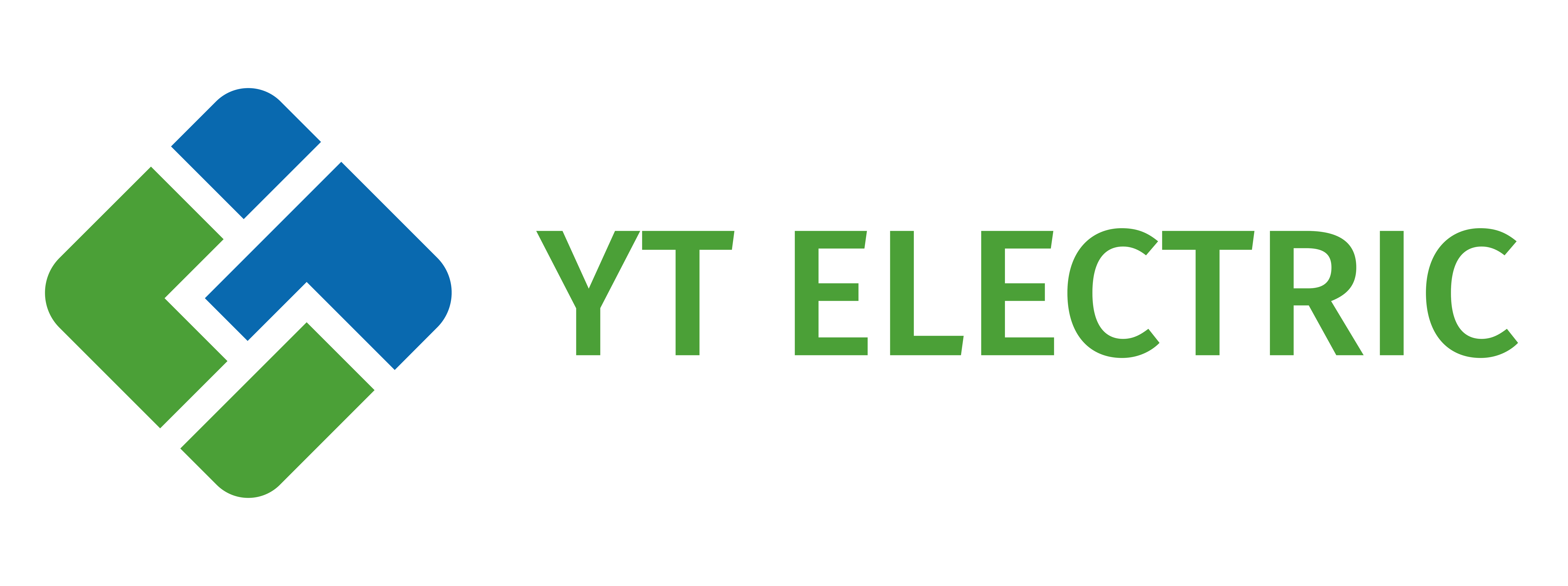
SMT mounter
SMT (Surface Mount Technology) is an electronic component installation technology used to attach electronic components (such as resistors, capacitors, integrated circuits, etc.) to printed circuit boards (PCBs). Compared to traditional plug-in technology, SMT patches have higher density, faster production speed, and lower production costs.
The working principle of SMT patches is to stick electronic components onto the surface of a PCB through molten solder, and then melt and fix the solder through methods such as hot air or infrared radiation. SMT chip technology is widely used in the field of electronic product manufacturing, such as Consumer electronics such as mobile phones, televisions, computers, as well as automotive electronics, medical equipment and other fields.
SMT patch technology has the following advantages:
1. Improve production efficiency: High degree of automation, fast processing speed, suitable for mass production.
2. Increase the density of the circuit board: Due to the direct placement of components on the surface of the PCB, more components can be accommodated in limited space, increasing the complexity of the circuit.
3. Reduce product volume: Due to the small and tightly arranged components, the product size can be smaller.
4. Reduce production costs: reduces the process steps of plugins and reduces labor and material costs.
5. Improve reliability: The connection of patch welding is stronger and more stable, and can better resist environmental vibration and temperature changes.
In summary, SMT chip mounting technology is widely used in the electronic manufacturing industry and has become one of the main processes in modern electronic product production.
Wave Soldering
Wave soldering is a surface mount technology for electronic components, used to solder electronic components onto printed circuit boards (PCBs). DIP packaged components (such as integrated circuit chips) can be installed on printed circuit boards (PCBs) through sockets or socket strips. These DIP packaged components have the characteristic of pins arranged in a double row straight line, allowing them to correspond to sockets and be inserted into PCBs. During the wave soldering process, electronic components that have already been pre coated with solder paste are fed into the preheating area through a conveyor belt, and then pass through the wave soldering furnace area. In the soldering furnace area, a "peak" is formed by spraying molten solder alloy upwards, which coats the solder alloy onto the pins of DIP packaging components to achieve welding connections.
YTPQC-SVG/AHF
YTPQC-AHF(Active harmonic filter)、SVG (Static Var Generator) mainly use 5th insulated gate bipolar transistor (IGBT) to control the magnitude and phase of inverter AC voltage, so as to achieve the purpose of harmonic filtering , reactive power compensation and 3 phase load balancing .
In terms of reliability, due to the lack of popularity, the reliability of the higher generation IGBT is lower than that of the lower generation IGBT.
The seventh generation IGBT has higher frequency and faster speed. Which will lead to smaller volume of other components used by it, so the overall volume of the module is smaller. For our industry, the main difference is product volume. In terms of product volume, we are currently developing a new 2U module, which has a considerable compensation capacity with a smaller volume
For more information about cost of Static Var Generator and Active Harmonic Filter, contact sales@yt-electric.com
Subscribe to us to enjoy event prices and get some of the best prices.